How Automated Riveting Machines Boost Productivity

Manufacturing is all about efficiency. Companies constantly look for ways to streamline production, reduce costs, and improve quality. When it comes to fastening components, riveting is a crucial process. But traditional riveting methods can be slow, inconsistent, and labor-intensive. That’s where automation comes in.
By integrating an automated riveting machine, manufacturers can significantly increase speed, precision, and efficiency. These machines take over the manual process, ensuring consistent results with minimal human intervention. If you want to enhance productivity, reduce errors, and optimize your workflow, let’s explore why automated riveting machines are a game-changer.
1. What Is an Automated Riveting Machine?
An automated riveting machine is a specialized system designed to perform riveting operations with minimal human input. Unlike manual or semi-automatic methods, these machines:
- Position rivets accurately every time.
- Apply consistent force, reducing material damage.
- Speed up production while maintaining quality.
Used across industries like automotive, aerospace, electronics, and furniture, these machines revolutionize the assembly process.
2. Faster Production Speeds
Speed matters in manufacturing. Manually placing and fastening rivets takes time and effort, leading to production bottlenecks. Automated riveting machines:
- Process multiple rivets in seconds, reducing cycle times.
- Eliminate the need for manual adjustments, keeping workflows smooth.
- Maintain consistent output, ensuring faster order fulfillment.
With higher speeds, companies can meet increasing market demands without compromising quality.
3. Improved Accuracy and Consistency
Manual riveting often leads to misalignment, uneven pressure, and defects. These errors not only waste materials but also increase rework and rejection rates. Automated riveting machines:
- Ensure precision by accurately placing and securing rivets.
- Deliver uniform pressure, reducing structural weaknesses.
- Eliminate human error, guaranteeing consistent product quality.
When every rivet is placed exactly as required, product integrity improves.
4. Reduced Labor Costs
Hiring and training workers for manual riveting can be expensive. Plus, repetitive tasks can lead to fatigue, mistakes, and injuries. By investing in an automated riveting machine, businesses can:
- Cut labor costs by reducing manual handling.
- Allocate employees to higher-value tasks, increasing overall efficiency.
- Minimize workplace injuries, reducing downtime and compensation claims.
Automation doesn’t replace workers—it helps them focus on more strategic roles.
5. Enhanced Workplace Safety
Riveting requires force, precision, and repetitive motion, making it a common source of workplace injuries. Automated systems improve safety by:
- Reducing human involvement in high-risk tasks.
- Minimizing exposure to sharp or hot materials.
- Eliminating repetitive strain injuries caused by manual riveting.
A safer work environment leads to higher employee satisfaction and productivity.
6. Lower Material Waste
Errors in manual riveting often result in damaged parts, misaligned components, and wasted materials. Automated riveting machines help by:
- Placing rivets accurately, reducing the risk of material wastage.
- Ensuring controlled pressure, preventing damage to delicate components.
- Optimizing material usage, leading to cost savings.
Less waste means better efficiency and increased profitability.
7. Adaptability for Different Applications
One of the biggest advantages of automated riveting machines is their flexibility. These machines can:
- Handle different rivet sizes and materials.
- Be programmed for multiple applications, reducing setup time.
- Integrate seamlessly with existing production lines.
Whether you’re assembling automotive parts, electronic casings, or aircraft structures, automation provides a tailored solution.
8. Consistent Product Quality
Product quality determines a company’s reputation and customer trust. Inconsistent riveting can lead to weak joints, failures, and recalls. Automated riveting machines ensure:
- Reliable performance, reducing product defects.
- Uniform fastening, preventing structural weaknesses.
- Compliance with industry standards, ensuring long-term durability.
Higher quality products mean fewer customer complaints and stronger brand loyalty.
9. Integration with Smart Manufacturing
With the rise of Industry 4.0, automation is more than just a productivity booster. Automated riveting machines can:
- Connect to IoT systems, providing real-time production data.
- Monitor machine health, reducing unexpected breakdowns.
- Enable predictive maintenance, improving overall equipment efficiency.
By integrating automation with smart manufacturing technologies, businesses stay competitive and future-ready.
10. Faster Return on Investment (ROI)
While automated riveting machines require an initial investment, the long-term benefits outweigh the costs. Businesses experience:
- Higher production output, leading to increased revenue.
- Lower labor and operational expenses.
- Reduced downtime and maintenance costs.
With improved efficiency and reduced waste, companies recover their investment faster than expected.
Final Thoughts
An automated riveting machine is more than just a tool—it’s a productivity powerhouse. From faster production and improved accuracy to cost savings and workplace safety, the advantages are undeniable.
If you’re looking to boost efficiency, reduce errors, and stay ahead in manufacturing, investing in an automated riveting solution is the way forward.
What's Your Reaction?
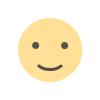
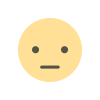


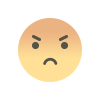
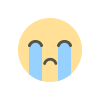
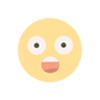